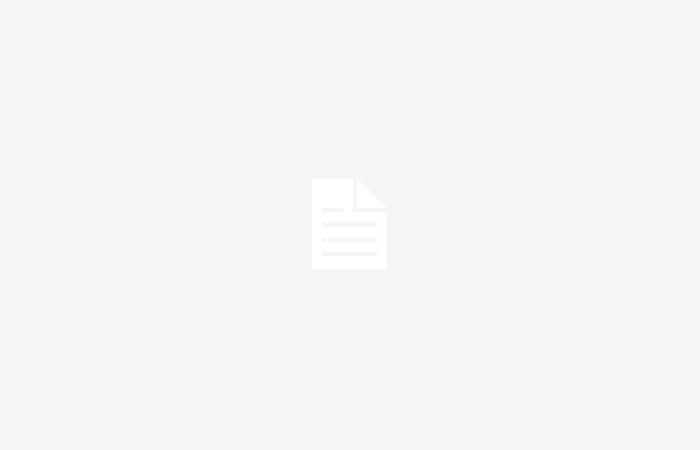
The Imola Autodrome is the first in the world to benefit from a green, innovative and sustainable asphalt, made with specially selected recycled hard plastics (such as some types of toys, fruit crates and old CD cases) and graphene for the activity of repaving of the access road to the Paddocks, solicited by the movements of heavy vehicles and people during the events and races scheduled on the Autodrome calendar such as the Formula 1 GP.
There innovative technology completely made in Italy is patented and developed by Iterchemistry – Italian company from Suisio (BG) specialized in sustainable solutions for the road sector – always committed to sustainability and green transition – and is the result of six-year research conducted by the Bergamo company in collaboration with G.Eco of the A2A Group, the University of Milan-Bicocca and Directa Plus, also a Lombard company producing graphene.
The use of Gipave guarantees greater performance in terms of resistance and durability, increasing the useful life of the flooring compared to the best technologies currently used on the market and strongly reduces environmental impacts thanks also to a less maintenance required. In particular, from a circular economy perspective, the technologies adopted reduce energy consumption and raw materials and products and are used reusable materials And completely recyclable.
“Motor racing is an essential part of Italian sporting culture and the Imola Autodrome fully represents its excellence by hosting one of the most prestigious races of the Formula 1 World Championship – he has declared Federica GiannattasioCEO of Iterchimica – We are therefore particularly proud to contribute to making an area such as that of the Paddock access road more green and sustainable with our innovative and completely made in Italy technology, active and operational even on race weekends, such as for example from 17 to 19 May when it will host the teams and fans for the Emilia-Romagna Grand Prix”.
“We decided to asphalt from the Rivazza entrance to the Paddock because it is the part most subjected to the transit of heavy vehicles” – he has declared Peter BenvenutiGeneral Director of the Imola Autodrome – “For us, sustainability is important, we are a certified circuit for sporting and sustainable events. The repaving is a first step for us to experiment with this technology, with the aim of also being able to intervene on the resurfacing of the track through this innovative process which can also be an example for other racetracks in the world”.
Thanks to the intervention on the access road to the Paddocks of the Autodrome, over the useful life of the pavement, savings have been estimated equal to: more than 78,000 kg of bitumen, equal to the weight of approximately 46 cars, 1.623 million kg of aggregates (corresponding to the weight of 955 cars), approximately 115 truck trips used for the transport of materials, over 1,182,125 kWh of energy (equal to the monthly needs of approximately 5,254 families) and 74,000 kg of CO2eq (equivalent to the absorption action of approximately 3,000 adult trees in a year). In addition, 3,700 kg of recycled hard plastics were recovered.
As regards the project data, Gipave was used for the 5 cm wear layer (for 3700 m2) and for the 10 cm binder layer (for 1300 m2). For both the wear and binder layers, 15% of “milled” material deriving from the demolition of old flooring was used. In addition to this, sand recovered from slag was used (12% for wear and 20% for the binder). The adhesion activator Iterlene IN 400-S was also used.
This product improves the adhesion between bitumen and aggregates, prolonging the useful life of the pavement. In addition to this, it gives greater workability during the production cycle, facilitating compaction and also increasing the wettability of the aggregate by the bitumen. These performance qualities are suitable for multiple areas of use, from urban roads to airport runways. Furthermore, Gipave has been certified as PSV (Second Life Plastic) technology and the EPD (Environmental Product Declaration) was finalized in 2023. The quality of the materials is supervised by the University of Bologna both during the production and laying phase and in the post-production phase.
From 2018 to today, Gipave has been used both in Italy and abroad. In particular, for the road surface of the new Genoa San Giorgio bridge, for the taxiways of the Rome-Fiumicino and Cagliari-Elmas airports, the A4 Brescia-Padua motorway, the internal transit areas of the a2a Brescia waste-to-energy plant and the repaving of the lane most subjected to heavy traffic on the A4 Turin-Milan motorway.
The company CTI (Cooperativa Trasporti Imola SCRL) of Imola collaborated and carried out the work (for the milling, production and laying phases).
© all rights reserved
published on 04/23/2024
Tags: Imola racetrack world green high tech asphalt graphene recycled plastics